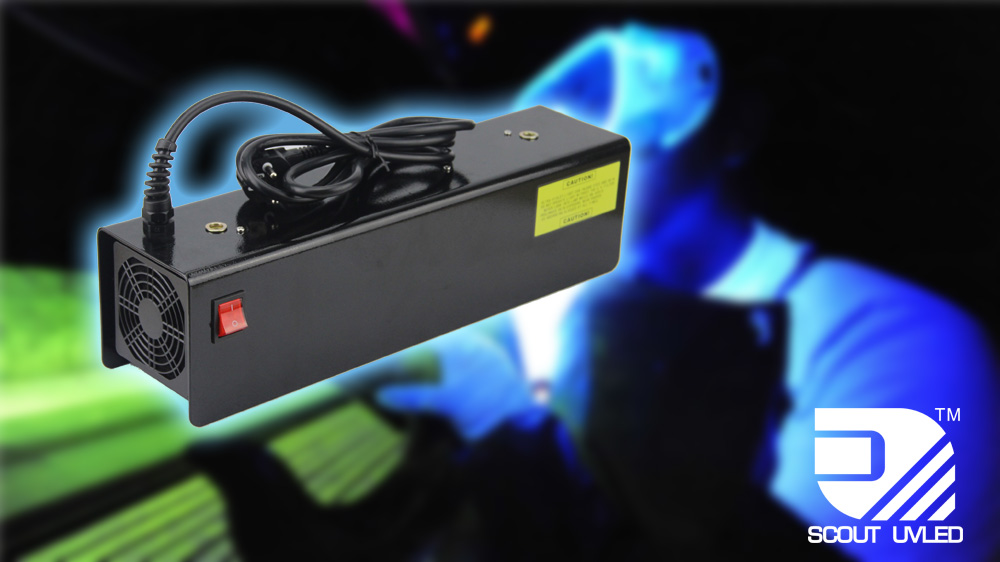
Nowadays, high-pressure mercury vapor arc lamps (hereinafter referred to as hot source black light lamps) can no longer meet the needs of green environmental protection. The LED UV-A black light is highly efficient and stable, and can directly convert electrical energy into light energy. It has two electrodes, allowing only a single direction of current flow, no oscillating current. Compared with the hot light source black light, LED black light can be turned on and off, and has a longer service life. LED UV-A black light lamps have a trend to replace traditional hot source black light lamps in the non-destructive testing industry.
1. UV Classification
Infrared, visible light, ultraviolet light, and X-rays are produced when the outer electrons, inner electrons, and nucleus of an atom are excited, respectively. Infrared, visible light, ultraviolet, and X-rays are all electromagnetic waves, which are produced in different ways and have different wavelengths.
In the draft international standard for limiting solar irradiance, the division of the UV spectrum (by range) is shown in Table 1, with the smaller the wavelength, the greater the energy. In the standard ASTM E 3022 “Standard Specification for Measurement of Emission Characteristics and Technical Requirements for LED-UVA Blacklight for Fluorescence Penetration Detection and Fluorescent Magnetic Particle Detection”, ultraviolet light is divided into three categories according to wavelength: UV-A, UV-B, and UV-C (see Table 1, 1 eV = 1.602 × 10-19 J).
- UV-A: Long-wave UV-A wavelengths of 320 ~ 400 nm, with strong penetrating power, can penetrate most transparent glass as well as plastic, and can also penetrate special colored glass that completely cuts off visible light. Fluorescence penetration testing, fluorescence magnetic particle testing with a black light filter, only emits near-ultraviolet light centered at 365 nm.
- UV-B: Medium-wave UV-B with a wavelength of 280~320 nm, medium penetrating ability, the shorter part of the wavelength is absorbed by transparent glass
- UV-C: Short-wave UV-C with a wavelength of 100~280 nm has the weakest penetrating ability and cannot penetrate most transparent glass and plastic.
UV Spectrum Division Table 1 |
||
---|---|---|
Name | Wavelength Range (nm) | Energy (eV) |
Long-wave UV | 320~400 | 3.10~3.94 |
Near UV | 300~400 | 3.10~4.13 |
Medium-wave UV | 280~320 | 3.94~4.43 |
Medium UV | 200~300 | 4.13~6.20 |
Short-wave UV | 100~280 | 4.43~12.4 |
Far UV | 122~200 | 6.20~10.2 |
Vacuum UV | 100~300 | 6.20~12.4 |
Light UV | 88~100 | 12.4~14.1 |
Extra UV | 10~150 | 8.28~124 |
Extreme UV | 10~121 | 10.3~124 |
2. Principle of LED UV-A Black Light
The traditional hot light source black light produces a glow discharge from the starting electrode, causing the mercury to evaporate, ionize, and produce an arc between the two main electrodes, the arc light emits the main peak of the ultraviolet spectrum at about 365 nm. That is, in compliance with the electron transition principle, the electron of the atom returns to the fundamental state from the excited state, emitting electromagnetic waves of different wavelengths, the electron excited state of the mercury atom and the fundamental state of the energy difference just in the ultraviolet range.
LED UV-A black light is established on the basis of semiconductor light emitting, after adding forward voltage to the light emitting semiconductor, the hole injected from the P region to the N region and the electron injected from the N region to the P region, within a few microns near the PN structure, respectively, with the N region of the electron and the P region of the hole compound to produce spontaneous radiation of ultraviolet light.
The spectrum emitted from the hot source black light is continuous, the spectrum fluctuation is larger than the LED black light, the stability is not as good as the LED black light, and the spectrum emitted from the LED black light is narrower, can be used for curing.
3. Auxiliary Structure of LED UV-A Black Light
1) Structure
The LED UV-A black light is mainly composed of light-emitting diodes, integrated circuit boards, filters, lenses and lamp housings. Light-emitting diodes are used as LED light sources, that is, lamp beads. The length, width, and illumination angle can be adjusted according to actual needs to realize point light sources, line light sources, and surface light sources to meet the illumination process requirements of different detection occasions. The real pictures of overhead LED UV-A black light and handheld LED UV-A black light are shown in Figure 1.
The LED black light IC board is designed to be flexible, allowing you to change the number of light beads and their arrangement, add a white light source to achieve the conversion between black and white light, and switch the circuit on at will. That is, the integrated circuit can realize digitalization, intelligent control and information transmission and other functions.
2) UV-A Pass Filter
The spectrum emitted by black light is very wide. The visible light with wavelength above 400 nm will produce bad lining on the surface of the workpiece and make the fluorescence display not sharp; the short-wave black light with wavelength below 320 nm will hurt human eyes; the black light filter material is dark purple glass, which only allows the light with wavelength from 330 to 390 nm to pass, and the light of other wavelengths will be filtered out.
The filter has a double insurance function, one is to prevent harmful light sources, the second is to protect the lamp beads from environmental pollution. a certain type of filter used in LED black lights, the transmittance of the spectrometer test as shown in Figure 2, the visible lamp beads emit UV after filtering again, the UV-B band below 280 nm is basically non-existent.
3) Lens
The purpose of the LED black light using a lens is to make the light beads emit different angles of light energy concentration together, in order to facilitate the implementation of the test, do not use a lens will emit different angles of the light spot and the formation of scattered light, the emitted light illumination is low, can not meet the detection requirements.
Figure 3 shows the comparison of the spot display under the irradiation of three types of LED black light, of which Figure 3 (A), (B) shows the spot uniform, Figure 3 (C) shows the spot is not uniform. Using the black light illuminance meter to measure the different areas of the spot in Figure 3(C), there are differences in the black light irradiance, which may cause missed detection in the actual detection process.
In summary, it can be seen that selecting the lens and adjusting the illumination angle is the key to ensuring the uniformity of the LED UV-A black light spot.
4. Common Problems and Solutions in the Use of LED Black Light
1) Quality audit control points
In the past various types of quality audits, penetration testing audit items most, mainly focused on the content of documents, materials and hardware supporting the requirements of the LED black light mainly the following three points:
① Provide black light manufacturer issued on the UV light source can effectively output the correct peak wavelength, the normal output of the peak wavelength (365 ± 5) nm verification.
② Black and white illuminance meter calibration period and accuracy, maintenance requirements.
③ Portable (battery-powered) LED black light use, maintenance, light intensity stability requirements, and in the use of the process, in order to effectively monitor the illumination decay, to prevent leakage, before and after the use of black light irradiance must be measured.
Requirements on LED UV-A black light should be reflected in the relevant procedural documents, detailing the content of the above 3 requirements, in addition to on-site operations to meet the requirements of the document.
2) Error caused by measurement
The measurement of black light irradiance and white light in the test darkroom environment needs to record the measured value. In actual operation, the test value is prone to deviation, especially the test of ambient white light. The main reasons are the following two categories:
① Influence by the visible light meter
Test visible light probe reflection, Figure 4 shows the two models of visible light meters test white light probe light reflection comparison, can be seen a probe than b probe has obvious reflection, will cause deviation of test data.
② External interference and improper operation influence
Different UV-A and visible light dark room test results are shown in Figure 5, the normal measurement of visible light display as shown in Figure 5(a), the error caused by the measurement is mainly reflected in the following aspects:
- Affected by the reflective material in the darkroom, such as plastic foam, the corresponding visible light display 27.99 lux [see Figure 5(b)], which has exceeded the standard 20 lux
- The tested visible light probe was contaminated with fluorescent substance (penetrant), as shown in Fig. 5(c), corresponding to the visible light showing 27.02 lux.
- The gloves stained with penetrant reflect visible light under UV-A light, as shown in Figure 5(d), corresponding to the visible light shows 9.90 lux, which meets the standard, but the actual recorded test value has been distorted.
- The light-colored work clothes reflected visible light under UV-A light, as shown in Fig. 5(e), and the test value was 8.40 lux, with obvious deviation.
3) Solutions
① Keep the dark room clean and tidy, do not allow superfluous things, clear the room of reflective substances and fluorescent substances, etc., so that it is away from the black light a certain distance.
② The probe for testing UV-A and visible light should not be touched with your hands or other contaminants. Keep the surface of the probe clean. It must be kept properly after use.
③ When testing, you cannot wear gloves with reflective and fluorescent substances, and you need to wash your arms or put on clean black silk gloves before entering the dark room.
④ When testing, the operator should stand away from the probe, to avoid light-colored clothing in the black light reflection, while it is recommended to change to dark or non-reflective clothing into the dark room test.
5. Material Failure
The main effects of the failure of LED UV-A black light materials are as follows:
1) Lamp bead illumination decay
After a period of time, the luminous efficiency of the lamp beads will be reduced to a certain extent, causing the black light irradiance decay, when the irradiance can not meet the requirements should be timely replacement of the lamp beads.
2) Filter rupture
Filter rupture will cause the black light wavelength shift; if the filter is contaminated by the external environment will reduce illumination, then use alcohol spray on the dust-free cloth, and then wipe the filter with a dust-free cloth.
3) The filter is oxidized
The high temperature of the lamp body will cause the black light spectrum drift, so in the design of LED black light, you need to add heat sink or choose the material with its own heat dissipation function.
4) Lamp body temperature is too high
The high temperature of the lamp body will cause the black light spectrum drift, so in the design of LED black light, you need to add heat sink or choose the material with its own heat dissipation function.
5) Lens aging
The aging of the lens will cause the black light irradiance decay, the wavelength will also be shifted, so when the lens is aging, the lens should be replaced in time.
When checking the illuminance of the black light lamp, it is necessary to pay attention to the changes in the test data and compare it with the data of the previous cycle test. If the value changes greatly, it should stop using it, and conduct a comprehensive quality management comprehensive analysis to find out the cause of the deviation.
6. Conclusion
As more and more LED UV-A black light into the market, black light hardware technology and performance continue to improve. LED black light is the most frequently used equipment for fluorescent magnetic particle inspection and fluorescent infiltration inspection, and its high efficiency and stability is the cornerstone to ensure the quality of inspection work.